ARMY TM 10-1670-282-23&P
AIR FORCE TO. 13C5-30-2
NAVY NAVAIR 13-1-33
2-7.
Checking Unpacked Equipment After Shipment.
a.
Inspect equipment for damage incurred during shipment. If the equipment has been damaged, report the
damage on SF Form 364, Packing Improvement Report.
b.
Check the equipment against the packing slip to see if the shipment is complete. Report all discrepancies in
accordance with the instructions in DA PAM 738-750.
c.
Check to see whether the equipment has been modified.
Section III. ASSEMBLY
Paragraph
Page
2-8
Assembly of the 34-Foot Cargo Parachute............................................................................................. 2-8
2-8.
Assembly of the 34-Foot Cargo Parachute.
NOTE
The procedure for assembling components of parachute is incorporated in the packing
procedure, paragraph 2-16.
Section IV. PREVENTIVE MAINTENANCE CHECKS AND SERVICES (PMCS)
Paragraph
Page
2-9
PMCS Procedures .................................................................................................................................. 2-8
2-9.
PMCS Procedures. The following describe PMCS procedures on the unit and intermediate direct support (DS)
maintenance levels.
a
General. Table 2-1 lists preventive maintenance checks and services. The purpose of PMCS is to ensure
that the 34-foot cargo parachute is operational.
b.
Frequency of Performing PMCS. PMCS will be performed before equipment is packed for use, during
modification and repair, after use, or at any time deemed necessary by the air delivery equipment maintenance officer.
c.
PMCS Columnar Fntries Table 2-1. Enter data in columns as follows:
(1) Item number The item number column shall be used as a source of the item number required for the
"TM Number" column on DA Form 2404 (Equipment Inspection and Maintenance Worksheet) when recording the
results of PMCS
(2)
IntervaL This column identifies the required PMCS level.
(3)
Item to be inspected. Contains the common name of the item to be inspected
2-8
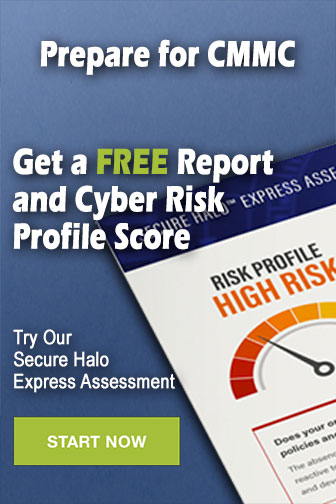