ARMY TM 10-1670-275-23&P
AIR FORCE TO 13C5-25-2
NAVY NAVAIR 13-1-26
2-13. Inspection (cont).
(c) Operational adequacy. Check item components and parts to insure proper assembly, which
includes attachment and alinement, and that assembled product functions in prescribed manner. Further insure
that no stitch formation or sewn seam has been omitted.
(d) Markings and stenciling. Inspect each assembly and components for faded, illegible,
obliterated, or missing informational data, identification numbers.
(e) Foreign material and stains. Inspect each assembly and related components for presence of
dirt or similar type foreign material. Also check for evidence of mildew, moisture, oil, grease, pitch, resin, or
contamination by salt water.
(2) Detailed inspection. In addition to the overall inspection performed in (1) above, a detailed
inspection will be performed on materials which constitute assembly or component construction using the
following criteria, as applicable.
(a) Metal. Inspect for rust, corrosion, dents, bends, breaks, burrs, rough spots, sharp edges,
wear, deterioration; damaged, loose, or missing safety pins.
(b) Cloth. Inspect for breaks, burns, cuts, frays, holes, rips, snags, tears; loose, missing, or
broken stitching or tacking; weak spots, wear, or deterioration.
(c) Fabric tape, webbing, and cordage. Inspect for breaks, burns, cuts, frays, holes, snags,
tears, incorrect weaving, and sharp edges formed from searing; loose, missing, or broken stitching, tacking,
whipping, and weaving; weak spots, wear, and deterioration.
(d) Pressure-sensitive (adhesive) tape. Inspect for burns, holes, cuts, tears, weak spots;
looseness and deterioration.
d. In-Storage Inspection. An In-storage inspection is a physical check conducted on a random sample of
air delivery equipment which is located in storage. The purpose of the inspection is to insure that the
equipment is ready for issue, that the item Is properly identified and segregated from other types of equipment,
that no damage or deterioration of equipment has been incurred, and that all modifications or similar action
requirements have been completed The inspection shall also concern the methods and procedures applied to
the storage of air delivery items, the adequacy of storage facilities, efforts of pest and rodent control, and
protection against unfavorable climatic conditions. Air delivery equipment which is in storage will be inspected
at least semiannually and at more frequent intervals if prescribed by the local parachute maintenance officer.
The frequency of inspection may vary according to the type of storage facilities and local climatic conditions.
In-storage inspection will be conducted only by parachute rigger personnel designated by local parachute
maintenance officer.
e. Equipment Disposition. Air delivery equipment may be rendered unserviceable by either normal fair
wear or by aging and will subsequently be repaired, modified, or condemned, as appropriate. Equipment that is
uneconomically reparable (outdated) will be condemned. Disposition of air delivery equipment that is
condemned, unserviceable, or for which the serviceability is questionable, will be accomplished using the
following procedures, as applicable.
(1) Item requiring repair or modification. An air delivery item which requires repair or modification will be
tagged in accordance with TB 750-126. Subsequent work on the item will be performed at the maintenance
level specified for the maintenance function in the applicable supporting technical publication.
2-18
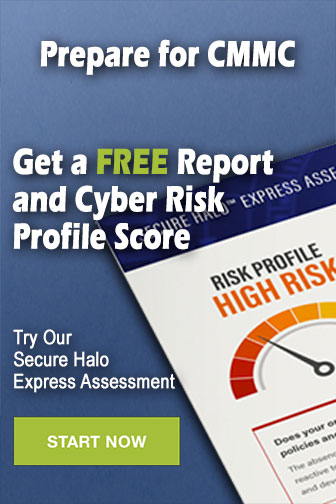