TM 10-1670-286-20
EXTRACTION LINE PANEL 0002 00
UNIT MAINTENANCE INSTRUCTIONS FOR EXTRACTION LINE PANEL
0002 00-1
REPAIR PARTS, SPECIAL TOOLS, TMDE, AND SUPPORT EQUIPMENT
COMMON TOOLS AND EQUIPMENT. For authorized common tools and equipment, refer to the Modified Table
of Organization and Equipment (MTOE) applicable to your unit.
SPECIAL TOOLS, TMDE, AND SUPPORT EQUIPMENT. No special tools, TMDE, or support equipment is used
in the Extraction Line Panel.
REPAIR PARTS. No repair parts are authorized.
SERVICE UPON RECEIPT
Upon receipt of a Extraction Line Panel, it will be given a Technical/Rigger type inspection to ascertain the
following:
Assembly Completeness. Insure that the applicable assembly is complete and no parts are missing.
Insure that no stitch formation or sewn seam has been omitted.
Inspect each item for faded, illegible, obliterated, or missing identification markings, which are part number,
manufactures name and date of manufacture.
Inspect each assemble for the presence of dirt, or similar type foreign material, also check for evidence of mildew,
moisture, oil, grease, pitch, resin, or contamination by salt water.
Inspect for breaks, burns, cuts, fray, holes, snags, tears, incorrect weaving, and sharp edges formed from searing,
loose, missing, or broken stitching, weak spots and deterioration.
PREVENTIVE MAINTENANCE CHECKS AND SERVICES (PMCS) PROCEDURES
Table 1 provides a logical arrangement of maintenance checks and services. The purpose of PMCS is to assure
you that the Extraction Line Panel is operational.
PMCS will be performed before equipment is packed for use and after use, or at any time deemed necessary by
the airdrop equipment maintenance officer.
PMCS column entries in Table 1.
The item number column shall be used to identify the item shown in figure 2 and required for the TM Number
column on DA Form 2404, Equipment Inspection and Maintenance Worksheet when recording the results of PMCS.
Interval. This column identifies the required PMCS interval.
Item to be inspected. Contains the common name of the item to be inspected.
Procedures. Provides a brief description of the procedure by which the check is to be performed.
Record all defects discovered during the inspection.
Inspection Function Requirement. Normally, airdrop equipment maintenance personnel at a packing,
rigging or repair activity would perform a technical/Rigger-type inspection. The item will be placed in proper
layout on packing table or suitable sized area. Should defect be discovered at any point during the inspection,
the inspection will be terminated and the applicable item will be processed and forwarded for cleaning and
replacement.
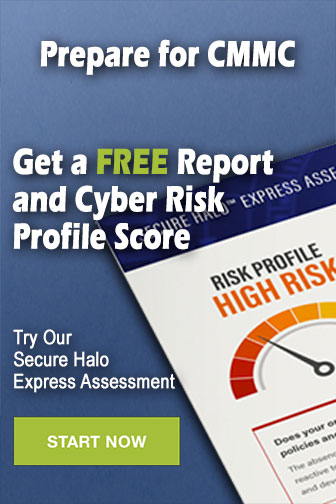