TM 10-1670-299-20&P
TO 14D1-2-470-2
NAVAIR 13-1-41
Section I. REPAIR PARTS; TOOLS; SPECIAL TOOLS; TEST MEASUREMENT AND
DIAGNOSTIC EQUIPMENT (TMDE); AND SUPPORT EQUIPMENT.
2-1. COMMON TOOLS AND EQUIPMENT. For authorized common tools and equipment, refer to the Modified Table of
Organization and Equipment (MTOE), CTA 50-970, or CTA 8-100, as applicable to your unit.
2-2. SPECIAL TOOL, TMDE, AND SUPPORT EQUIPMENT. The tool and test equipment requirements required for the
maintenance of the Personnel Troop Parachute Ancillary Equipment are listed in Appendix B, Section III., Tool and Test
Equipment List.
2-3. REPAIR PARTS. Repair parts for the Personnel Troop Parachute Ancillary Equipment are listed and illustrated in
Appendix C, Repair Parts and Special Tools List.
Section II. LUBRICATION INSTRUCTIONS
2-4. GENERAL. Apply a limited amount of "zipper ease" lubricant to the slide fastener on any ancillary equipment
component when it becomes difficult to operate.
Section III. SERVICE UPON RECEIPT
2-5. UNPACKING. When items are received, inspect packaging before unpacking and note any obvious damage. If
package is ripped, torn or exhibits evidence of water or heat damage, do not accept item. Prepare a Standard Form 368,
Quality Deficiency Report as described in paragraph 1-10.
2-6. SHIPPING MATERIAL. When unpacking equipment, avoid ripping and tearing packaging materials more than
necessary. Save crates, boxes and barrier material so that it can be re-used.
2-7. CHECKING UNPACKED EQUIPMENT. Check unpacked equipment for physical damage and evidence of water
stains. Check that unpacked equipment is complete and all parts are present. Prepare a Standard Form 368, Quality
Deficiency Report as described in paragraph 1-10 if damage or shortages are noted. The unpacked items will be
inspected by a qualified rigger (MOS-43E) . The inspection performed will be a technical/rigger type as outlined in
paragraph 2-14.
2-2
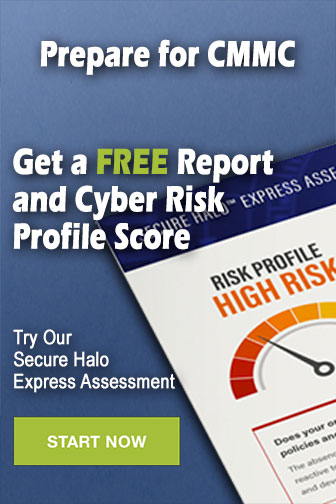