TM 10-1670-287-23&P 0005 00
0005 00-2
b. Attach a 7-pound weight to ripcord grip and suspend weight from handle, exercising care to apply
the load gradually without impact. The hands or lifting device, as applicable, must be fully
removed from the weight.
NOTE
A ripcord-locking pin will withstand a 7-pound load without assuming
a permanent set.
c. Remove weight, rotate locking pin one-quarter turn, and test pin again by reapplying the load as
prescribed in step b.
d. Repeat the procedure in step c. until locking pin has been tested in four positions and rotated
one-quarter turn prior to each test.
NOTE
Each locking pin on a ripcord length will be tested under load in four
positions.
e. Remove weight from ripcord grip and remove locking pin from test block.
f.
Visually examine the tested locking pin to ascertain if it was marred, cracked, or distorted during
the test under load. If any defects are noted, remove ripcord from service.
g. Repeat procedure in steps b. through e. for the remaining locking pins on the ripcord length.
After testing all locking pins, if there are no visual defects apparent, test each of the locking pins
for bends.
h. Place locking pins in vertical position with pin end facing up and either clamp the pin between two
wooden blocks at a point below the shoulder (as shown in B of the illustration on the previous
page) or hold between the thumb and index finger of one hand.
i.
Using test gage, manually locate the hole in the block over the end of the secured pin, allowing
for a 1/16-inch maximum insertion.
j.
With axis of the gage block hole aligned with axis of the locking pin, release gage block and allow
block to fall freely.
k. When the weight of the gage block fails to cause full penetration of the pin into gage block hole,
the pin is excessively bent. Remove ripcord from service.
l.
Repeat the procedures in steps h. through k. for each of the remaining locking pins on the ripcord
length.
m. Position ripcord grip on a fixed hook from a corner nearest weld.
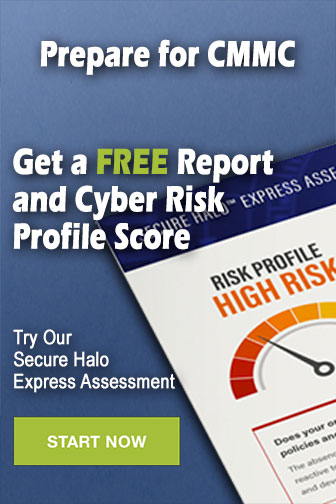