TM 10-1670-292-23&P 0003 00
0003 00-2
Configuration Condition. Acceptance of new equipment from the manufacturer is based upon
inspections made of sample lots that have been randomly selected in accordance with military standards.
It is incumbent upon the using activity personnel to bear this in mind whenever equipment is first placed in
service. Changes will sometimes evolve from the original equipment design and sometimes contractors
are authorized deviations in material and construction techniques. Air delivery equipment that has been in
the field cannot be expected to meet exacting manufacturing specifications; however, the equipment
should closely reflect desired design characteristics. Since repairs, modifications, and/or changes can
alter or detract from the configuration originally desired, such equipment shall be airworthy, safe, of the
desired configuration, and adequate for intended use.
Marking Parachutes. Prior to being placed into service, personnel parachutes that have had no previous
use will be marked to reflect the date of entry into service. The marking will be made on the canopy
information data block by stenciling the lettering in ½-inch characters, using the marking and restencilling
repair procedures detailed in WP 0014 00. Other applicable parachute components will be marked
adjacent to existing data. The stenciled data will appear on IN-SVC followed by the date, which will
indicate the month and calendar year, such as "Jan. 85". Ensure the added marking does not infringe
upon, or obliterate, any original data on the information data block.
Marking Risers. Prior to being placed into service, the risers will be marked to reflect placed in service
and identified as a MC1-1C/MC1-1D. Mark each riser with two turns blue; ½-inch pressure sensitive
adhesive tape, around each riser assembly, centered on the confluence wrap.
Position Control Lines. For new MC1-1C/MC1-1D parachutes being placed in-service and in-serviced
parachutes with less than six jumps, position control lines as follows:
1. Trace each control line bridle and the attached control line from the point of attachment to the canopy
to the free-end of the control line.
2. Pass the control line free-end from the top, through the channel guide ring (located on the inside of
each rear riser), and further past the control line free-end, through a wood toggle. (Refer to WP 0026
00 for toggle construction details, if required).
3. Position the toggle against the bottom of the guide ring and, while holding the toggle in position, pull
the control line free-end taut until the control line tension equals that of the suspension lines. Move
each toggle three inches from the channel guide ring. While holding each control line in position,
place one-inch wide masking tape on the control line just above the toggle, wrapping the tape around
the riser once. Do not remove this tape.
4. Make two overhand knots in each control line against the bottom of each toggle. The remaining free
end of each control line from the second overhand knot is to measure five inches. Then make the
third overhand knot in the free end. Trim the control line free end at a point ½-inch below the third
overhand knot.
5. For parachutes with more than five jumps, position the control line toggles according to the following
procedure.
a. Undo the three overhand knots in each control line free end.
b. Pull both control line free ends until control line tension equals that of the suspension lines.
c. Follow the procedures given in WP 0026 00.
6. Annotation will be made in the note section of the parachute log record that the control line toggle
adjustment procedure has been performed.
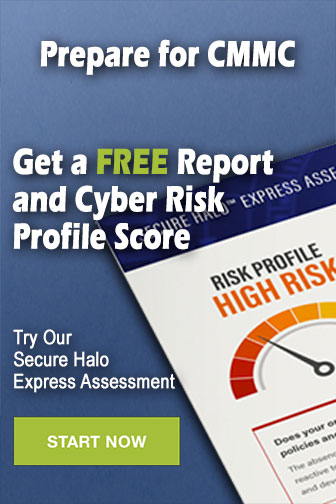