TM 10-1670-296-20&P 0004 00
0004 00-3
Inspection Function Requirement. Normally, air delivery equipment maintenance personnel at a
rigging activity will perform a technical/rigger-type inspection. The inspection of initial receipt items will be
performed as a separate function from the rigging activity; the item to be inspected will be placed in a
suitable sized floor area. Should defect or damage be discovered at any point during the inspection, the
inspection will be terminated and the applicable item will be repaired.
Should defect or damage be discovered at any point during the inspection, the inspection will be
terminated and the applicable item will be processed and forwarded to repair activity. The repair activity,
in turn, will conduct a technical/rigger-type inspection that will be performed by only those parachute
rigger personnel cited in AR 750-32.
DROP TESTING PROCEDURES
NOTE
Conducted only by authorized units.
Drop testing of airdrop equipment consists of physically air dropping an item from an aircraft in flight. The
drop test proves the serviceability of an item or checks parachute rigger proficiency. It will be performed
under the supervision of qualified parachute rigger personnel who satisfy the supervisory requirements
outlined in AR 750-32. Drop-testing usually will be conducted by an activity responsible for the inspection
and maintenance of airdrop equipment. The criteria required to accomplish a drop test is as follows:
Weight and Conditions. The weight of the test load will be proportional with the standard design load of
the specific parachute being tested. The parachute will be released under conditions consistent with the
requirements for an equipment drop.
Monitoring. During the drop-test of the LVADS, the deployment of the parachute will be thoroughly
monitored and observed to detect any evidence of malfunction or defect. Enter a record of the drop-test
into the applicable parachute log record as follows:
CHECKS AND SERVICES
Table 1 contains a tabulated listing of organizational preventive maintenance checks and services, which
must be performed by a qualified rigger.
Common Checks to the LVADS Ancillary Equipment. When you perform PMCS procedures, you will
always need a rag or two.
1. Remove debris with a dry stiff bristle brush.
2. Remove dirt and grease with a soap solution composed of one-half cup of dishwashing detergent per
gallon of water. Rinse with clean water. Wipe dry with a clean cloth.
3. Check equipment for rust and corrosion. If any bare metal or corrosion exists, clean, and apply a thin
coat of oil, unless otherwise stated. Report it to your supervisor.
4. Check all bolts, nuts and screws for obvious looseness, missing, bent, or broken condition. Look for
chipped paint, bare metal, or rust around bolts heads. If you find a bolt, nut or screw you think is
loose, tighten it or report it to your supervisor.
5. On welded items, look for loose or chipped paint, rust, or gaps where parts are welded together. If
you find a bad weld, report it to your supervisor.
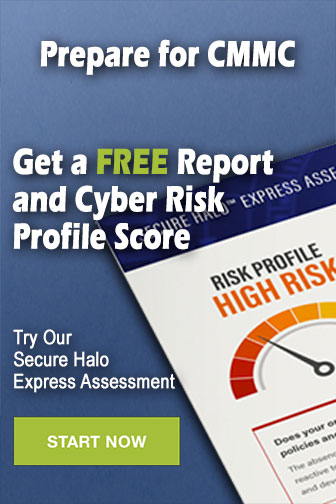