TM 10-1670-293-23&P
0005 00
T-10C/T-10D TROOP BACK PARACHUTE ASSEMBLY
PREVENTIVE MAINTENANCE CHECKS AND SERVICES (PMCS), INTRODUCTION
0005 00-1/(2 Blank)
GENERAL
The following describe PMCS procedures on the unit and direct support levels. The PMCS table has been
provided to ensure the T-10C/T-10D parachute is in proper operating condition, and ready for its primary
mission.
SCOPE
The following work packages (WP 0007 00 through WP 0037 00) contain maintenance procedures that are
the responsibility of the specified technician, as authorized by the Maintenance Allocation Chart (MAC), and
the Source, Maintenance, and Recoverability (SMR) coded items that are identified in the Repair Parts and
Special Tools List (RPSTL).
MAINTENANCE FUNCTIONS/PROCEDURES
Each of the mentioned work packages above identifies a maintenance function specified in the MAC. All
maintenance procedures required to complete a maintenance function are identified under This task
covers: in the order in which the work is most logically accomplished.
PARACHUTE REPACK INTERVAL
The T-10C/T-10D parachutes will be repacked at a scheduled interval to insure airworthiness. When
necessitated by climate/storage/use condition, the local airdrop equipment maintenance officer may require
more frequent repack intervals. In this regard, a major concern would be rapid fluctuations of temperature
(fluctuations around 32 degrees Fahrenheit, freezing point) sustained high or low temperature, or high
humidity and heavily polluted atmosphere. The T-10C/T-10D troop back parachute assemblies will be
repacked at a 120-day interval.
DROP TESTING CRITERIA
Drop-testing of the T-10C/T-10D troop back parachute assemblies consist of physically airdropping an item
from an aircraft in flight. The drop-test is used as a means of proving the serviceability of an item or
checking parachute rigger proficiency, and will only be performed under the supervision of qualified
parachute rigger personnel who satisfy the supervisory requirements outlined in AR 750-32. Drop-testing will
usually be conducted by an activity responsible for the inspection and maintenance of airdrop equipment,
which includes either parachute packing or airdrop load rigging. The criteria required to accomplish a drop
test is as follows:
1. To drop-test a troop-type personnel parachute, a qualified parachute rigger will jump the parachute and
he applicable type parachute will be released under conditions that are consistent with the requirements
for a personnel jump or equipment drop.
2. During the drop-test of any type parachute, the deployment of the parachute will be thoroughly
monitored and observed to detect any indication of malfunction or defect. A subsequent record of the
applicable parachute log record will be entered into the applicable log record using procedures outline in
WP 0003 00.
3. Any type of airdrop equipment that indicates evidence of malfunction/defect during, or after, a drop-test
will be disposed of as prescribed in WP 0009 00.
4. A personnel parachute that is considered to have contributed to the injury of an individual parachutist
(critical or fatal) will be disposed of in accordance with WP 0009 00, Equipment Disposition.
5. Airdrop equipment that does not reflect evidence of malfunction or defect upon completion of a drop-test
will be administered a technical/rigger-type inspection as outlined in WP 0009 00. If serviceable, the
item(s) may then remain in use.
END OF WORK PACKAGE
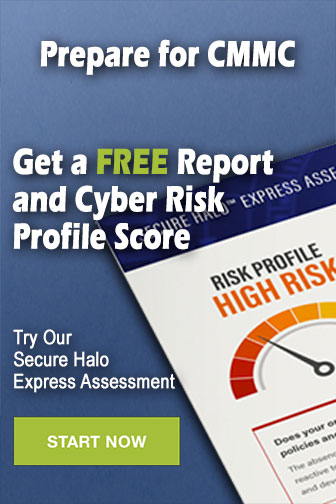